In 2017, Shell collaborated with industry, international institutions, non-governmental organizations, and academics to develop a set of Methane Guiding Principles.
In line with these goals, Shell developed a new well pad design for their Alberta Shales business in 2019, eliminating methane emissions from pneumatic devices by using instrument air. In late 2019, Shell decided to move forward with a trial of EPOD to optimize its instrument air design. A 20 kW EPOD was installed and commissioned on April 15, 2020, at one of their Alberta Shales multiwell pad sites.
EPOD fills a void that existed in the power generation market for remote locations. The EPOD trial unit operated consistently and demonstrated a significant reduction of fuel gas consumption, GHG emissions, and maintenance costs.
David Hatch, Shell Facilities Engineer
Switching to instrument air and using EPOD resulted in a 1400 tCO2e/yr reduction in greenhouse gas emissions from previous gas pneumatic designs – the equivalent of over 300 cars off the road. This was accomplished through reduced power demand (elimination of oversize generator + load bank), elimination of venting from pneumatics and minimizing construction scope. In addition to improved environmental performance, Shell realized a 26% capital cost improvement and 85% operating cost reduction on its remote power generation design.
On the success of the trial, David Hatch, Shell Facilities Engineer, concludes, “The EPOD was installed safely and seamlessly, it operated consistently and demonstrated reduced maintenance costs. It also significantly reduced our fuel gas consumption, further reducing the well pad design GHG emissions. The compact and modular design of the utility system will allow us to reduce our construction schedule providing direct improvements to HSSE and construction cost.”
The success of this trial has resulted in the adoption of the EPOD in all future well pads in Shell’s Alberta Shales operations.
To request the full case study, please click here.
On the success of the trial, David Hatch, Shell Facilities Engineer, concludes, “The EPOD was installed safely and seamlessly, it operated consistently and demonstrated reduced maintenance costs. It also significantly reduced our fuel gas consumption, further reducing the well pad design GHG emissions. The compact and modular design of the utility system will allow us to reduce our construction schedule providing direct improvements to HSSE and construction cost.”
The success of this trial has resulted in the adoption of the EPOD in all future well pads in Shell’s Alberta Shales operations.
To request the full case study, please click here.
×
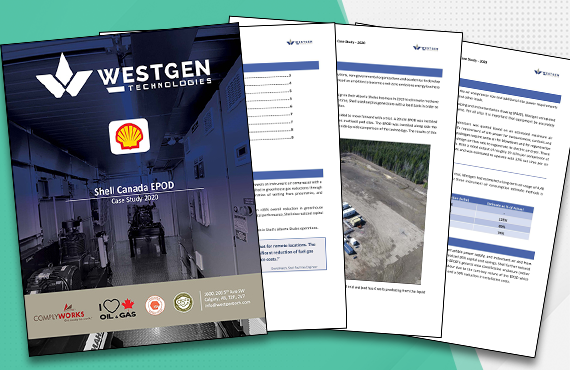